CityU in Hong Kong has invented the novel ceramic inks and developed the world’s first-ever 4D printing for ceramics combining 3D printing, self-shaping assembly and elastomer derived ceramics.
A new chapter of constructing geometrically flexible and mechanically robust ceramic structures is started from the City University of Hong Kong and it might have a big impact in the field of biomedical, space exploration, aircraft engine, military equipment and microelectromechanical systems. Origami-like 3D printed objects obtanied from the research group of Prof. Jiang Lu are generate by a process called Four-Dimensional (4D) printing.
A 4D printed object is referred to an object that has been printed using a 3D printing technology but that is able to transform over time due to inherent properties of the material. Polymer-derived ceramics (PDCs), prepared through thermolysis of polymeric ceramic precursors, exhibit remarkable properties of conventional ceramics such as high thermal stability, chemical resistance to oxidation and corrosion, in addition to mechanical resistance to surface forces. The microstructures and properties of PDCs can be tuned through tailored polymer systems and thermolysis conditions.
How do we achieve the fourth dimension?
The invention, showed in a paper published on the Science Advances journal and protected by the patent number US10377076B2, described anew process for the 4D printing. The object is obtained by extruding inks through a nozzle directly on a heating plate, which compacts the material and creates a 3D preform. Then, the 3D-printed elastomer is folded into a complex structure to form a 4D-printed pre-strained elastomeric object and converting it into the 4D-printed ceramic final product.
Inks composition
One element in the inks consists of inorganic oxide nanoparticle, containing at least one of zirconium, calcium, aluminium, titanium, indium, zinc and silicon dioxide. As an alternative, aluminium nitride particles, calcium silicate particles, silicon carbide particles, polymeric particles, metallic particles, carbon black particles, graphene particles and graphite particles can be used as well as the oxides. The polymeric ceramic precursors in the inks include at least one of poly dimethylsiloxane, polysil sesquioxanes, poly carbosiloxanes, poly carbosilanes, polysil carbodiimides, polysil sesquicarbodiimides, polysil azanes and polysil sesquiazanes. The temperature of the heating plate is in the range of 30°C-400°C, the folding of the object is achieved by metal wires, finally the polymer-to-ceramic transformation occurs via pyrolysis in a vacuum or under an inert atmosphere with a heating temperature of 400-2000°C.
As far as you can image
As proof of the capacities of this method, representative ceramic origami structures with complex curvatures were built from 3D-printed cuboid or precursors, obtaining objects mimicking a butterfly, the Sydney Opera House, a rose and a dress.
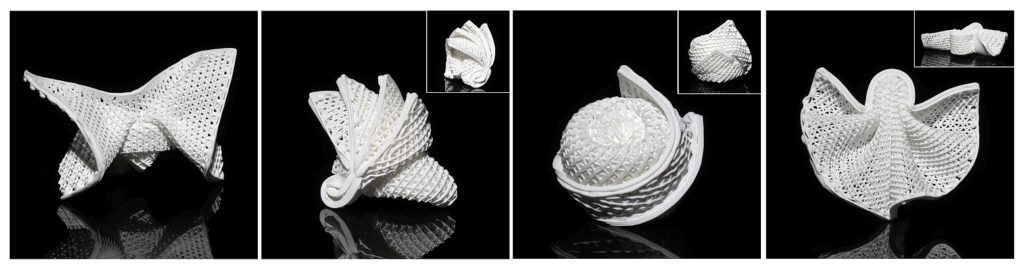
The printed periodic local patterns in elastomeric lattices improve the foldability of global structures and guaranteed the programmability in locating constraints.
The invention described herein provide several advantages, i.e. objects with a high geometrical complexity can be created, having a high mechanical robustness, approximately 10 times higher than the conventional silica-based foam, moreover the strength-scalability synergy is demonstrated, meaning that the techniques and materials have great potential for industrial scale production. The materials and techniques used are based on commercially available systems, so they can be developed within short time having an immediate impact on the field.